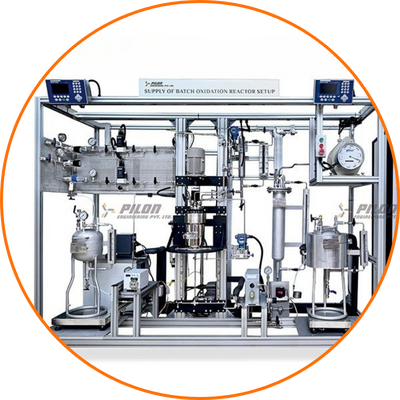
Batch Reactor System
Design and manufacturing of Batch reactor systems by Pilon Engineering is done in-house. Pilon’s batch reactor system are used for full vaccum upto positive pressure by any MOC like SS3116, Hastalloy, glass lined steel or borosilicate glass depending on chemical compatibility
- Batch Reactor systems that are easy to operate at elevated temperatures and pressures.
- Volume ranges from 25mL to 2000 Liters.
- MOC available Glass, Stainless steel, Inconel, Hastalloy, Incolloy (800, 800H and 800HT, Monel, Titanium etc.)
- Designed for proper mixing of the contents
Salient Features of Batch Reactors Systems:
- Contents are very well mixed, so the contents have relatively uniform properties such as temperature, composition, density, etc. throughout
- Working as high as 300 bar (g) and temperatures up to 1200 Deg. C.
- Batch reactor jackets enable precise heating or cooling by maintaining a constant jacket heat flux.
- Pilon batch reactors are versatile and designed for consecutive production of multiple products.
- The systems are designed in compliance with international standards like ASME, PED, and CE.
- Suitable for various area classifications like safe, explosive, atex various zones etc.
- System integration with PLC-SCADA is available, using reputable brands for piping, valves, gauges, controllers, sensors, furnaces, flow controllers, panels, and software—all procured and assembled in-house.
- Designed for easy assembly and maintenance with efficient layouts and user-friendly features.
- Easy feed loadings and unloading
- Low cost of construction, operation, and maintenance.
Continuous Stirred Tank Reactor System
Continuous stirred-tank reactors (CSTRs) are open systems, where reactants are free to enter or exit the system. They operate in a steady state condition Reactants are continuously introduced into the reactor, while products are continuously removed.
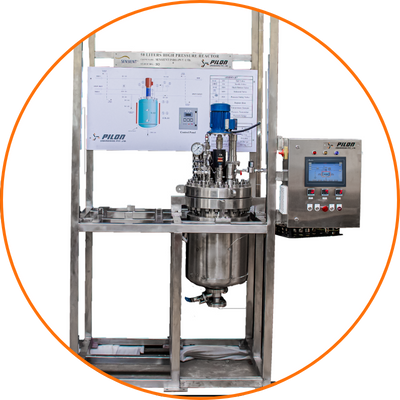
- Volume ranges from 25mL to 2000 Ltrs
- MOC available Glass, Stainless steel, Inconel, Hastalloy, Incolloy (800, 800H and 800HT, Monel, Titanium etc.)
- Designed for proper mixing of the contents
- Can be operated on different ranges of temperatures and pressures.
Salient Features of Continuous Stirred Tank Reactors Systems:
- Reactants are very well mixed, so they have relatively uniform properties such as temperature, composition, density, etc. throughout.
- Working pressures as high as 300 bar (g) and temperatures up to 500 Deg C.
- Multiple CSTRs can be used for immiscible or viscous liquids requiring high agitation rates.
- Reactors can be customized as per application needs and configured in series, parallel, or multitoned setups.
- Each system is designed in accordance with relevant international standards.
- Suitable for various area classifications like safe, explosive, atex various zones etc.
- Systems are automated using computer-based PLC and SCADA software’s.
- International Design and manufacturing standards followed.
- Systems are thoughtfully designed for easy assembly and low-maintenance operation
- Our systems are designed such that maintenance is easy and cost effective.
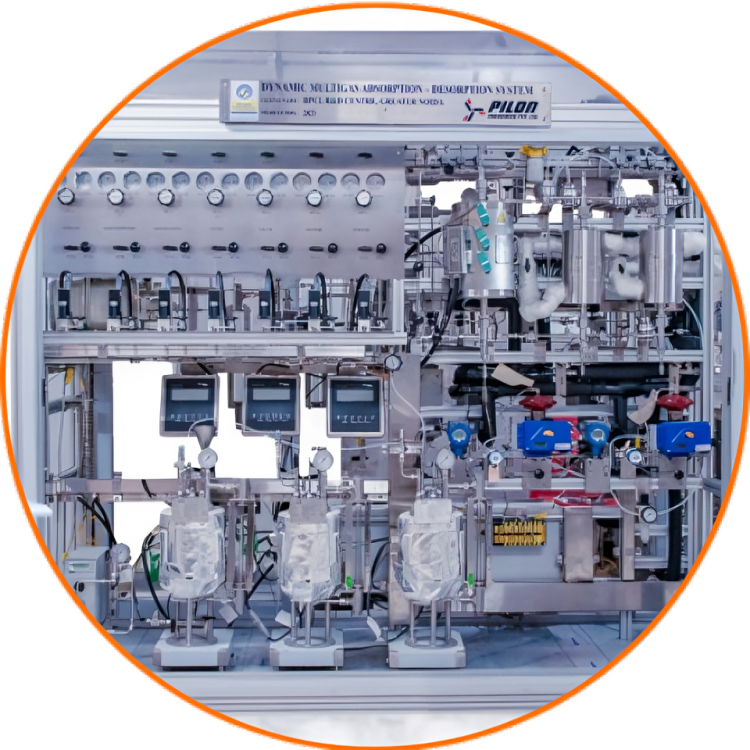
Fixed Bed Reactor System
Fixed Bed reactors designed and manufactured by Pilon Engineering have high Pressure and Temperature.
- Also known as FBR, these tubular reactors contain catalyst pellets and support uni-, bi-, or multi-conversion rate per catalyst weight compared to other catalytic reactors. Directional flow for reactant conversion
- At Pilon, we offer various catalyst configurations such as a single large bed, multiple horizontal beds, parallel packed tubes, and separate beds in individual shells
- Various configurations may be adapted depending on the need to maintain temperature control within the system.
- You may have pellets of various shapes and sizes i.e. spherical, cylindrical, or randomly shaped pellets. They range from 0.25 cm to 2.0 cm in diameter. Pilon helps accommodate them all.
Salient Features of Fixed Bed Reactor Systems:
- Available in volumes from 5 mL to 100 L, Pilon reactors handle up to 500 barg and 1200°C, with MOCs like Glass, SS, Inconel, Hastelloy, Incoloy (800 series), Monel, and Titanium. Customizable for series, parallel, or multizoned setups, all designs follow international standards and consider area classifications for maximum safety.
- Our systems feature in-house integration with PLC-SCADA using reputed components—piping, valves, gauges, controllers, thermocouples, furnaces, flow controllers, sensors, panels, and software. Thoughtful design ensures easy assembly, efficient catalyst loading/unloading, and enhanced reactant-catalyst contact, leading to 3. higher product yield. They perform effectively under high temperature and pressure, and close collaboration with our team ensures optimal system understanding and output.
Packed Bed Reactor System
A packed bed reactor is a hollow vessel such as a tube or pipe filled with packing material tailored to the specific application or service.

- The packing can be randomly filled with small objects like Ranching rings, saddle packing’s, or Pall rings, or use specially designed structured packing. At Pilon, we help you achieve the ideal packing solution.
- Our Packed beds may also contain catalyst particles or adsorbents such as zeolite pellets, granular activated carbon, etc.
- The purpose of a packed bed is typically to improve contact between two phases in a chemical or similar process.
- Packed beds are used in chemical reactors, distillation, scrubbers, and also for heat storage in chemical plants.
- Our PBRs are used in fine chemicals, oil & gas, petrochemicals, pharmaceuticals, pesticides, and research centers.
Salient Features of Packed Bed Reactor System:
- MOCs like Glass, Stainless Steel, Inconel, Hastelloy, Incolloy (800 series), Monel, and Titanium. They offer high catalyst conversion rates and customizable configurations—series, parallel, or multizoned.
- Designed and manufactured per international standards (PED, ASME, CE) and suitable for various area classifications (safe, explosive, ATEX zones). In-house PLC-SCADA integration uses reputable components for smooth assembly, easy maintenance, and simple catalyst/packing handling.
- Enhanced reactant-catalyst contact increases product yield, all at low construction, operation, and maintenance costs. Available in volumes from 5 mL to 100 L, Pilon reactors operate up to 500 barg and 1200°C with
Trickle Bed Reactor System
- Primarily used for hydrodesulfurization, Pilon specializes in trickle bed reactors where liquid flows downward over a catalyst bed, with pressure differences driving solid-liquid-gas contact

- In trickle bed reactors, fluid flows over catalyst particles forming fine films, rivulets, or droplets, while gas flows co-currently or counter-currently. They mainly operate continuously but can be semi-batch, offer low catalyst attrition, and work efficiently across various temperatures and pressures.
Salient Features of Trickle Bed Reactor System:
- Available in volumes from 5 mL to 100 L, Pilon reactors handle pressures up to 500 barg and temperatures up to 1200°C, with materials of construction including Glass, Stainless Steel, Inconel, Hastelloy, Incolloy (800 series), Monel, and Titanium.
- High conversion rates per catalyst weight are achievable. Reactors are customizable and can be configured in series, parallel, or multizoned setups. Pilon ensures all designs comply with international standards, regardless of system size.
Suitable for safe, explosive, and ATEX zone classifications. Pilon integrates fully automated PLC and SCADA systems, using reputable brands for piping, valves, and equipment. Designs ensure smooth assembly and easy maintenance with efficient layouts.
Micro Flow Reactor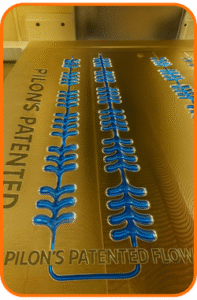
Micro Flow Reactors (MFRs) are compact, continuous flow systems used in chemical manufacturing. They offer precise control over reaction conditions, making them safer, more efficient, and scalable compared to traditional batch reactors.
Key Advantages
- Efficient heat and mass transfer due to high surface-area-to-volume ratio.
- Supports Chemistries Beyond Conventional Limits.
- Enhanced safety with small reaction volumes.
- Consistent product quality through precise control of reaction parameters.
- Scalable via scaling up or sizing up.
- Environmentally friendly with reduced waste and solvent usage.
- Enables Controlled Execution of Hazardous or Energetic Reactions.
Industrial Applications
- Fine chemical and specialty compound synthesis.
- Continuous production of high-value chemicals.
- Asymmetric synthesis for chiral compounds.
Examples
- Pharmaceutical Industry: Used for safe and efficient synthesis of Active Pharmaceutical Ingredients (APIs) and intermediates.
- Polymer Chemistry: Enables controlled polymerization reactions with consistent molecular weights.
- Agrochemicals: Applied in the synthesis of crop protection agents with reduced environmental impact.
- Specialty Chemicals: Applied in the synthesis of specialty chemicals with reduced environmental impact and enhanced safety.
Challenges
- Regulatory frameworks are often tailored to batch processes.